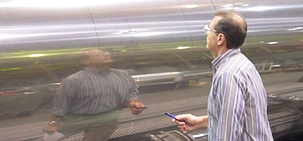
If you had to choose between achieving greater or lesser profitability, revenue and productivity, your decision would be a no-brainer. But real-life choices aren’t always so clear. Add in upfront, short-term costs, and it’s easy to lose sight of your desired long-term results. When it comes to precision grinding, the same holds true.
Roll grinding services are essential to achieving better product yield, reduced operational interruption and less downtime. But some companies choose to take on such a project internally, under the false assumption that it costs less than seeking out a roll maintenance expert.
If your rolls develop chatter, feedlines and barring, maintaining them to produce perfectly round and concentric cylinders is critical to your production.
Production Efficiency
To achieve maximum production efficiency, your rolls must have precise profile, shape, TIR and roundness. While it’s widely accepted that OEM specifications are the best a roll gets, they are actually the simple standard. Perfectly smooth and concentric rolls surpass the specifications of the OEM, and the benefits are immense.
With perfectly centered crowns 360 degrees around, not only does your machine run more smoothly and quietly, but the lifespan of your roll and its cover is significantly increased. If faultlessly maintained, your rolls require less grinding over time, which mitigates the risk of future downtime and lost production.
The exactness of the grinds, consistency of wear and uniform surface finish also ensure that your covers continue to produce quality products long after they’ve been maintained. Whether rubber, poly or composite, roll covers last longer and provide greater long-term value.
Such exact precision grinding and roll uniformity allows you to run your converting equipment faster – increasing your revenue and profitability. Only perfectly maintained rolls give you long-term production benefits. This is an impossible task for an in-house team. But expert surface grinders are trained to grind rolls to perfect specifications.
Cost Efficiency
When you think “expert,” “costly” might be the next word that comes to mind. It’s often the case that the best in any business charges a premium, and it might scare away some businesses. But the reality is that the cost of expert precision grinding is typically less than using a surface grinder in-house.
$600,000 – that is the annual cost to run the standard grinder with a four-man crew 24/7. When you consider the cost of electrical, lighting, supply, environmental, labor, benefits and other overhead, in-house roll maintenance exceeds half a million dollars.
Too often, managers focus on the obvious expenses of a project and fail to include the supplemental resources involved in analyzing the cost of completing a job. When comparing the financial outlay of outsourced precision grinding versus an internal team, don’t get hung up on the short-term cash flow. In the end, it’s very likely that enlisting an expert is actually the more prudent financial decision.
Roll projects are complex undertakings and require diligent analysis. Your machines are a long-term investment, so their maintenance should be treated accordingly. Before deciding how to maintain your rolls, weigh the benefits and drawbacks of both your future production and your all-encompassing expenditures.
It might surprise you, but the option that has a more significant and positive impact on your bottom line is apt to be the expert roll grinding services.