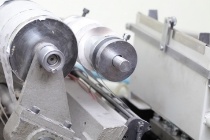
In the paper industry, manufacturing precision is essential to generating a high-quality product. You want to manufacture flawless paper that your customers are able to rely on.
But, if you’re working with rolls that have defects, it’s nearly impossible to keep your products up to standards.
Explore four common roll defects that paper manufactures face, as well as the negative impacts these flaws have on your products and how to repair them.
Barring
One of the most common manufacturing problems in the paper industry is barring, or variations in your rolls’ circumferential profile. Barring can run from one end of your roll to the other and prevents your final paper product from being uniform. This roll defect often increases the number of sheet breaks at your paper converters, and you often see the negative impact on your production efficiency.
Over time, your rolls experience regular wear and tear, which could lead to a nonuniform nip, or pressure between two rolls. If you don’t have a uniform nip, you won’t have a uniform product. To repair this issue, it is essential to have your rolls ground to perfection.
Loose Tolerances
In paper manufacturing, tight tolerances play a crucial role in generating a final product that meets your uniformity and quality standards. Rolls that aren’t up to par cause a number of problems, including defects in your final product, lowered production efficiency and increased maintenance costs.
Reduced tolerances will more quickly lead to increased vibration in your rolls. And, if you’re running your rolls at higher speeds than the manufacturer recommends, your path to runnability issues is hastened. Regularly grinding your rolls back to your the original tolerances or better eliminates these problems. If you are running rolls at higher speeds, you might need to tighten the allowed tolerances of your rolls up to 50%.
Feedlines
Like barring, feedlines are surface variations on your rolls. While barring refers to lines along the width of your rolls running parallel to its center of rotation, feedlines run around your roll. Picture the spiral of a barber pole – feedlines have a similar pattern.
Feedlines impact your final product the same way that surface variations from barring cause defects. This spiral pattern often slows down your sheet conversion and causes imprints on your paper, reducing your print quality.
Preventing and identifying feedlines on your rolls requires regular inspection and monitoring of product quality. When you identify feedlines, have your rolls ground to their original smooth surface and reinstalled to your tightness standards.
Lack Of Concentricity
In any industry involving rolls, manufacturers know that a lack of roundness hinders production efficiency. Perfectly round rolls are essential for manufacturing the best possible product. But, it’s often difficult to identify if your rolls aren’t perfectly round. You may visually inspect your rolls and think they are in good shape, but in reality, they may be misshapen.
If your rolls aren’t exactly concentric, the evidence turns up in your final product. Look for variations in your product to identify rolls that need to be ground back to perfect roundness.
To achieve your ideal roundness standards and eliminate the issues caused by all four of these roll defects, the smartest decision is to partner with a precision roll grinder who has the expertise and equipment to help increase your profitability and minimize downtime. This is the best way to ensure that you’re maintaining efficiency, manufacturing a high-quality product and keeping your clients coming back for business.