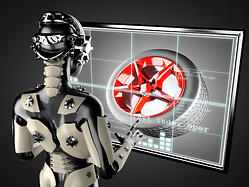
IBISWorld released its Tire Manufacturing market research report in July, unveiling its latest findings in the sector heavily tied to the rubber manufacturing industry. With roughly 31% growth over the last five years and the increasing prevalence of fuel-efficient tires and new innovations, your production efficiency and quality must meet the needs of your customers for you to succeed.
Many tire companies are pushing the envelope to develop more advanced products to set them apart from the competition. And like them, you must also set yourself apart from your competitors. Product quality uniformity is essential, but it cannot come at the cost of your production efficiency. Ultimately your profitability comes down to the quality of your rolls and the roll grinding process.
The Big Tire Innovations
Innovations in the tire industry are rampant of late. But three in particular are raising precision standards and quality of the rubber they use.
1) Goodyear is creating an “intelligent tire” that embeds a microchip inside its tires that relays information to the driver regarding tire pressure, temperature and ways to improve driving performance and safety.
2) Michelin’s Tweel airless tires, the winner of Equipment World’s Innovation award, are made from steel and rubber to guarantee no flats or blowouts.
3) Cooper Tire is introducing a tire that uses a tread design to better indicate its wear. A visual indicator transitions among five different stages to let a driver know when it’s time to replace their tires.
The Implications For Roll Grinding In Rubber Manufacturing
In the rubber industry, calenders are typically five roll stacks that don’t touch. Your roll profiles must be even – it is the most critical characteristic to your production efficiency and quality. With uneven profiles, your rolls produce an uneven product. And with recent innovations demanding absolute precision, this substandard simply doesn’t cut it.
Historically, rubber manufacturers have used the block grinding technique (grinding back and forth between two rolls with a flat bar), which cuts deeply into your bottom line. While your rolls may be smoother on the surface, you’re not removing their defects or ensuring that their profiles are uniform. In fact, you could be making the problem worse.